Geislinger’s Home Grown Talent Strategy Leads to Higher Retention and Productivity
By Ben Hoger, Michigan Works! Southwest
For individuals looking to start a career or advance in a career in manufacturing, Geislinger Corporation might be the answer. Located in Battle Creek, with a sales, service and manufacturing facility supporting North and South America, Geislinger Corporation provides direct sales support, technical and design assistance, manufacturing and service capabilities both in-house and on-site. They provide engineered coupling, damper, and shafting solutions that meet international quality standards, marine certifications, and quality requirements that optimize their customer’s systems and are BUILT TO LAST.
Only one position in the facility is considered a general utility position, the rest are skilled trade positions, meaning that specialized training is needed; and the best person to offer that training to an apprentice is someone currently performing the job.
According to Plant Manager Jason Woodard, Geislinger would like to have one to two apprentices a year if possible. To help make this happen, Geislinger works with the City of Battle Creek, Michigan Works! Southwest, Kellogg Community College, and the local high schools to recruit and train talent. They also organize tours, and participate in Manufacturing Day, where hundreds of students attend, according to Woodard.
For students who express an interest, Geislinger coordinates directly with staff at their school, and the students are invited to job shadow for a half a day. “Ideally, after that, we will bring one of those (students) on following their junior year” Woodard said. “Our goal is to have them return after graduation and go through the apprenticeship program.”
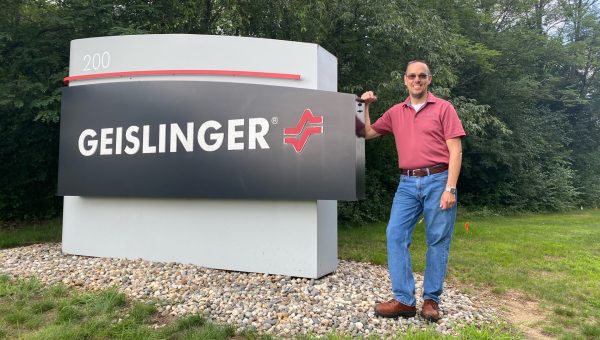